Moins de gaspillage et un travail plus fluide ? Apprenez à penser ‘Lean’ !
Comment avez-vous connu l’approche Lean ?
“J’ai travaillé 26 ans dans le secteur de l’automobile. En tant qu’ingénieur Process, ensuite comme ingénieur Qualité. Pour traiter les réclamations des clients, j’ai tout d’abord constaté que l’automatisation n’offrait pas toujours un processus exempt d’erreurs. C’est à la même époque qu’est apparu le concept Lean, dont Toyota était le fondateur, et il m’a été demandé de l’introduire dans l’entreprise. J’ai vu qu’il portait un potentiel énorme, mais aussi que beaucoup d’entreprises occidentales s’y prenaient mal.”
Christine remonte un peu les stores et me demande à quoi me fait penser le terme ‘Lean’. Ce qui me vient, c’est ‘Lean and mean’ (frugal et radin, NdlT). “Pas tellement positif tout ça”, dit-elle en riant. “Nous pouvons traduire ‘lean’ par ‘mince’, ‘frugal’. Les entreprises occidentales y ont tout d’abord vu un système pour réaliser des économies. Toyota n’a même jamais utilisé le terme de ‘lean’. Si vous appliquez avec succès la philosophie Lean, vous réduirez certains coûts, mais ce ne sera qu’une conséquence logique de ce choix et non un objectif en soi.”
La frustration a-t-elle été votre motivation pour vous lancer en tant que formatrice et coach ?
“Nous avons tous vu où nous mène l’obsession de réduire les coûts. Même dans l’entreprise où je travaillais, des usines ont été ouvertes à l’étranger. Tout d’abord au sud puis, une fois que c’était aussi devenu trop cher, en Europe de l’Est et en Chine. Je voyais encore tant d’opportunités de conserver quand même la production ici. Oui, le coût du travail est élevé, mais ce n’est qu’une partie du coût total.”
“Je voulais soutenir l’industrie de fabrication dans l’amélioration de ses process, sa manière de travailler. Pour sécuriser notre prospérité occidentale, ce qui deviendra rapidement un très gros défi, nous devons garder ici notre industrie de fabrication. C’est en créant des choses, en fabriquant des objets avec une valeur ajoutée, que vous créez un état de prospérité. J’ai nommé mon entreprise ‘Lean4Growth’ parce que le terme ‘Lean’ parle à beaucoup de gens mais, lors de mes formations, j’explique tout de suite que je préfère parler de ‘flow’.”
Le bien est l’ennemi de l’excellence. Il faut arriver à un processus permanent dans lequel vous allez sans cesse vous demander ce qui pourrait peut-être aller encore mieux
Que faut-il comprendre exactement par ‘flow’ ?
“Nous voulons créer un bon flow, une belle circulation de matériel et d’information mais, surtout, faire entrer les collaborateurs dans ce flow (flux) afin qu’ils se rendent au travail avec plaisir. En impliquant vos équipes dans le processus, vous les motivez, et vous pouvez ainsi changer quelque chose de manière effective et durable dans vos processus de production et d’information. Lorsque les coûts baissent, c’est une conséquence logique du processus. Si une entreprise met trop fortement l’accent sur ce point, je vois souvent se produire les choses les plus folles et qui, étrangement, aboutissent à ce que les coûts remontent à long terme.”
Comment cela fonctionne-t-il concrètement ?
“Prenons l’exemple d’un constructeur d’aménagements intérieurs, qui veut transformer le plus rapidement possible ses panneaux en élément de cuisine finis, parfaits, et ce sans nécessité de contrôles ni de corrections. Pour arriver à cela, il faut éliminer tous les obstacles du chemin. Dans l’approche Lean, on parle des sept gaspillages. Il faut tout d’abord apprendre à les repérer, car nous sommes généralement si habitués à faire les choses d’une certaine manière que nous ne réalisons pas que celle-ci n’est peut-être pas la meilleure. Il faut donc étudier tous vos processus à la loupe, d’un œil critique. Et cela concerne aussi bien la rédaction de devis, la gestion des stocks, la facturation, le planning, la production et la communication, bref, tous les éléments du processus.”
“À ce niveau, le bien est l’ennemi de l’excellence. Il faut arriver à un processus permanent dans lequel vous allez sans cesse vous demander ce qui pourrait peut-être aller encore mieux. Il ne faut jamais rester immobile. Si vous pensez que vous faites déjà bien à ce niveau, vous n’allez plus jamais vous améliorer. Avec le Lean, vous vous formez pour apprendre que les choses peuvent toujours être mieux faites.”
“Une fois que vous avez identifié les gaspillages, différents outils vous permettent de vous y attaquer, comme par exemple 5S, Standaard Werk, kanban, SMED ou TPM. Il est surtout important de comprendre la base de ce genre d’outils pour pouvoir les manier efficacement. Durant un trajet, nous allons nous y mettre de manière très concrète, dans l’atelier même. Et, encore plus important, il faut veiller à ce que les changements entrepris soient pérennes. Ce qui constitue un défi, car on revient toujours rapidement à la situation antérieure.”
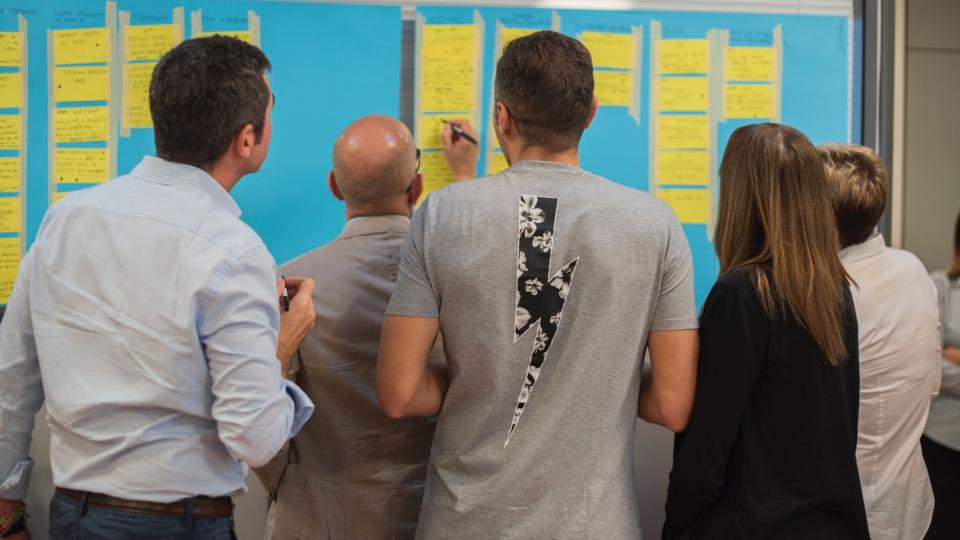
Je medewerkers betrekken is cruciaal
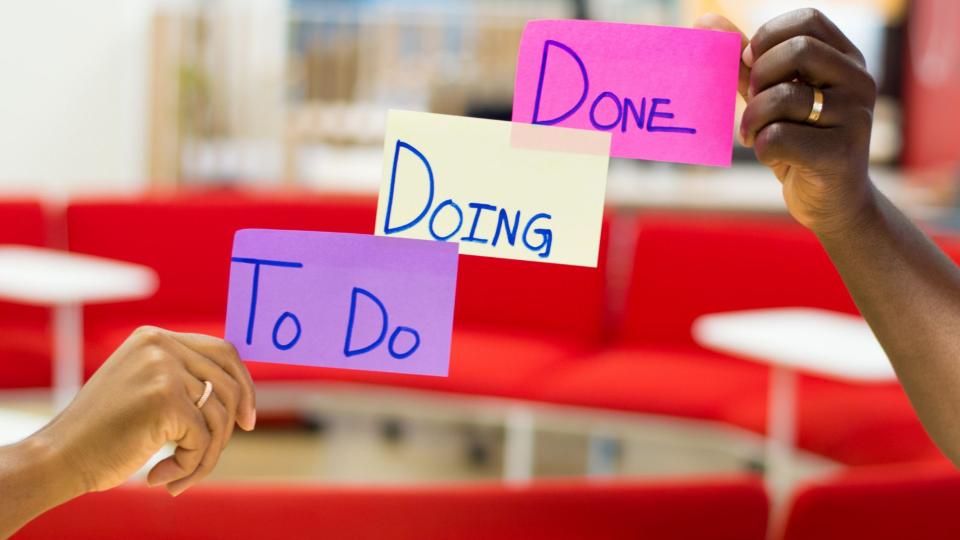
Breng flow in je processen
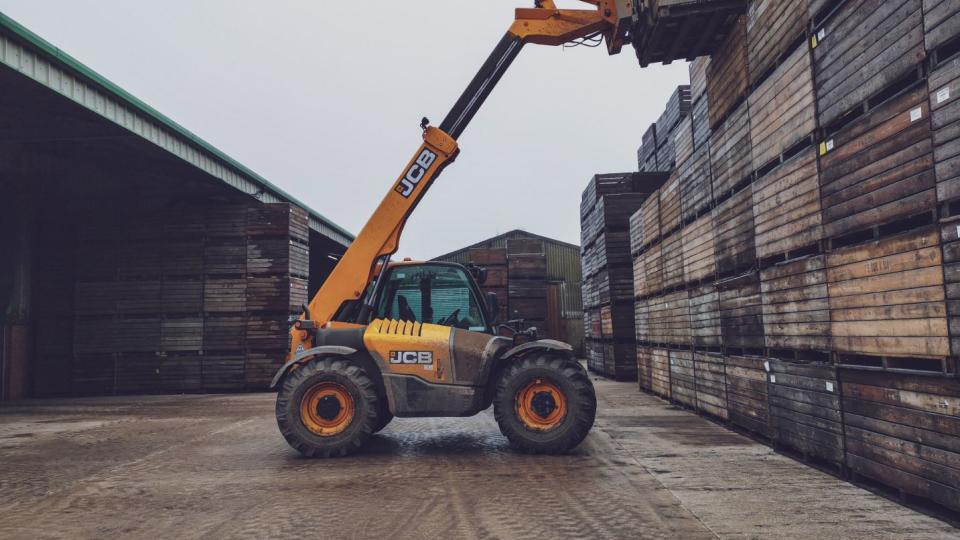
Zorg voor minder verspilling, verbeter de doorstroom van materialen
Comment s’assurer que les changements soient pérennes ?
“C’est seulement lorsque vous parvenez à entraîner les collaborateurs dans le flow que les changements pourront durer. C’est là que se trouve le savoir, au cœur de l’atelier.”
“On y parvient en impliquant les collaborateurs à chaque étape du processus. Vous ne pouvez pas vous imaginer ce qu’on obtient en retour ! Vous exposez le problème, vous donnez quelques principes de base et ils sont partis. Certains responsables sont plus rapides que d’autres, et il est très important de conserver une attitude de coaching. Durant un trajet, nous organisons des sessions au cours desquelles nous prenons toute une journée avec les collaborateurs, dans l’atelier de l’entreprise, pour faire et expérimenter des choses.”
Imaginez qu’en tant que professionnel, je veuille franchir le pas vers l’Industrie 4.0. Y a-t-il un moment idéal, dans un tel trajet, pour s’approprier cette philosophie ?
“Chacun peut y trouver son intérêt à tout moment, mais le mieux, en règle générale, avant est de franchir le pas avant d’investir. J’ai souvent vu des entreprises changer complètement leurs projets d’investissement après un training. Elles se rendaient alors compte qu’investir dans tel outil ou telle machine ne résoudrait pas tous les problèmes, ou bien elles voyaient d’autres solutions qui coûteraient probablement moins cher.”
Christine est pour une automatisation bien pensée. “Il faut trouver une bonne base, or même des entreprises telles que Toyota et Volvo ont fait un pas en arrière dans le domaine de la robotisation, parce qu’il manquait le cerveau humain lorsqu’il y avait des problèmes à résoudre. Et cela, un robot ne le peut pas. En revanche, il peut simplifier le travail.”
On investit bien trop souvent dans des logiciels qui font beaucoup de choses dont vous n’avez pas besoin. On vous dit qu’il faut adapter vos processus au logiciel, alors qu’en fait, c’est le contraire.
Donc, vous commencez par simplifier le processus, puis vous investissez dans des logiciels et des machines ?
“Il faut avant tout très bien savoir comment on veut travailler. Ce n’est qu’une fois que vous avez mis les process en carte et que vous les avez optimisés que vous réfléchissez à la façon de les soutenir. Tout d’abord, on investit bien trop souvent dans des logiciels qui, certes, font beaucoup de choses, mais qui font surtout beaucoup de choses dont vous n’avez pas besoin. On vous dit qu’il faut adapter vos processus au logiciel, alors qu’en fait, c’est le contraire. Il faut commencer par mettre de l’ordre dans vos bases, et c’est seulement ensuite que vous pouvez rechercher les systèmes et les outils qui conviennent.”
Quel type de problèmes l’approche flow peut-elle résoudre ?
“Elle peut par exemple vous aider à raccourcir les délais de fabrication, afin que vous puissiez effectivement livrer un projet au moment prévu. Vous apprenez à optimiser vos stocks, car vous ne voulez pas en avoir trop d’avance. Vous allez aussi minimiser les erreurs, par exemple une erreur de mesures, l’emploi d’un élément qui ne convient pas, ou encore un oubli de passer commande, ou d’emporter certaines choses sur le chantier. Il y a parfois trop de mouvements sur un chantier, ce à quoi nous répondons en adaptant la configuration du site de production.”
Etant donné la situation actuelle, ne faut-il pas conseiller aujourd’hui de garder des stocks réduits au minimum ?
“C’est un réflexe humain que de vouloir disposer de davantage de réserves, surtout lorsque vos voisins le font aussi, mais c’est ainsi qu’on déclenche un effet boule de neige. En stockant plus que ce dont vous avez besoin, vous créez des ruptures d’approvisionnement, ce qui fait monter les prix. On est presque obligé d’agir ainsi aujourd’hui, mais cela vous coûte le double. La première fois, parce que votre argent est bloqué dans votre stock, et la deuxième parce que les prix vont ainsi continuer à augmenter.”
L’approche ‘flow’ est-elle déjà installée dans le secteur de la menuiserie ?
“Elle y est encore relativement peu connue alors que, surtout du côté des PME, on peut très rapidement enregistrer des résultats positifs. Souvent, plus une entreprise est grande, moins les process sont efficaces, et plus les problèmes sont nombreux. La communication est difficile et les réactions trop lentes. On trouve typiquement les RH, la finance, l’engineering, la production, la qualité, etc., tous ces départements étant séparés par des murs épais. Et souvent, avant même que vous ayez obtenu les différents accords pour pouvoir vous attaquer aux problèmes, il est trop tard. C’est non seulement le cas des entreprises, mais aussi des écoles, et même des communes. Les petites entreprises sont plus maniables.”

Optimaliseer de bewegingen op de vloer
Tout l’art consiste à parvenir à prendre une certaine distance, pour avoir une vision d’ensemble, et à libérer du temps pour une réflexion stratégique
Devons-nous interpréter ceci comme un plaidoyer contre la croissance ?
“Bien sûr que la croissance a du bon, mais il faut procéder de la bonne manière. C’est là qu’on arrive au principe QRM, Quick Response Manufacturing. Vous constituez dans votre organisation de plus petites équipes, qui travaillent de manière autonome et peuvent même prendre des décisions. C’est ainsi qu’on reste maniable.”
Les menuisiers travaillent dur et sont souvent très impliqués dans le processus de production. Est-ce un piège ?
“Il est souvent incroyablement difficile pour eux de libérer du temps pour ce type de formation. J’ai vu des gens tellement surchargés qu’ils travaillaient jour et nuit et n’arrivaient toujours pas à tout faire. Tout l’art consiste à parvenir à prendre une certaine distance, pour avoir une vision d’ensemble, et à libérer du temps pour une réflexion stratégique. Comment allons-nous améliorer certaines choses, et dans quelle direction allons-nous ? D’autre part, il n’y a certainement rien de mal à être fortement impliqué. On comprend alors très bien la situation réelle.”
Il faut alors trouver des gens à qui vous pouvez confier le travail. Le manque de personnel joue-t-il un rôle ?
“Il constitue en effet un défi énorme. La philosophie Lean vous permettra certes d’avoir besoin de moins d’heures de main-d’œuvre pour effectuer le travail. Vous ne demanderez plus à vos équipes d’effectuer des tâches qui n’apportent aucune valeur ajoutée, mais de travailler aussi efficacement que possible. Vous aurez donc moins rapidement besoin de personnel supplémentaire mais, si vous en avez besoin, vous aurez du mal à en trouver aujourd’hui. C’est ainsi hélas !”
Lire cet article gratuitement ?
Il suffit de créer un compte gratuitement.
-
Lire quelques Plus articles gratuits chaque mois
-
Choisissez vous-même les articles que vous souhaitez lire
-
Restez informé via notre newsletter