Minder verspilling en meer flow op de werkvloer? Leer Lean denken!
Hoe ben je zelf met het Lean denken in aanraking gekomen?
“Ik heb 26 jaar in de automotive sector gewerkt. Eerst als process ingeneer, en later als kwaliteitsingenieur. Bij het behandelen van de klachten van klanten zag ik voor het eerst dat automatiseren niet altijd een foutloos proces oplevert. Rond die tijd begon het Lean gedachtegoed, waarvan Toyota de grondlegger is, zich te verspreiden en werd mij gevraagd om het in het bedrijf te introduceren. Ik zag dat er enorm veel potentieel in zat, maar ook dat veel Westerse bedrijven de bal missloegen.”
Christine draait even de rollen om en vraagt me waar ik aan denk als ik de term ‘Lean’ hoor. ‘Lean and mean’ is wat als eerste in me opkomt. “Dat klinkt al niet zo positief hé”, lacht ze. “We kunnen het vertalen als ‘slank’ en ‘mager’. Westerse bedrijven zagen het vooral als een systeem om te besparen. Toyota heeft de term ‘lean’ zelf nooit gebruikt. Als je de Lean filosofie succesvol toepast, zal je kosten besparen, maar het is dan een logisch gevolg en niet het doel op zich.”
Was die frustratie je drijfveer om als trainer en coach verder te gaan?
“We hebben allemaal gezien waar een te grote focus op kostenreductie ons brengt. Ook in het bedrijf waar ik werkte, werden er fabrieken in het buitenland geopend. Eerst in het Zuiden, en toen ook dat te duur werd, in Oost-Europa en China. Ik zag nog zoveel opportuniteiten om de productie toch hier te houden. Ja, de arbeidskost is hoog, maar het is slechts een deel van de totale kost.”
“Ik wilde de maakindustrie gaan ondersteunen in het verbeteren van hun processen, hun manier van werken. Als we onze Westerse welvaart veilig willen stellen, en dat wordt binnenkort een heel grote uitdaging, moeten we onze maakindustrie hier houden. Het is door dingen te creëren, door dingen met toegevoegde waarde te maken, dat je een welvaartsstaat creëert. Ik heb mijn bedrijf ‘Lean4Growth’ gedoopt omdat de term ‘Lean’ bij de meeste mensen een belletje doet rinkelen, maar tijdens een training maak ik meteen duidelijk dat ik liever praat over ‘flow’.”
Goed is de vijand van uitstekend. Het moet een voortdurend proces worden waarbij je steeds weer gaat kijken wat nog beter kan.
Hoe moeten we dat begrip flow precies begrijpen?
“We willen een goede flow, een mooie doorstroom creëren van materialen en van informatie, maar vooral ook de medewerkers ‘in de flow’ krijgen zodat ze met meer plezier naar het werk komen. Door je mensen te betrekken bij het proces, raken ze gemotiveerd en kan je ook effectief en duurzaam iets veranderen in je productie- en informatieprocessen. Wanneer de kosten dan naar beneden gaan, is dat een logisch gevolg van het proces. Legt een bedrijf er te sterk de klemtoon op dan zie ik vaak de gekste dingen gebeuren, die er vreemd genoeg voor zorgen dat de kosten op langere termijn omhoog gaan.”
Hoe gaat het concreet in zijn werk?
“Nemen we het voorbeeld van een interieurbouwer, dan wilt die van zijn plaatmateriaal zo snel mogelijk een afgewerkte keukenkast maken, en wel zo dat het een perfecte kast is, die meteen van de eerste keer goed is zonder dat er controle of correctie nodig was. Wil je dat doen dan moet je alle hindernissen onderweg wegnemen. In Lean praat men over de zeven verspillingen. Eerst moet je die leren zien, want we zijn het meestal zo gewoon om dingen op een bepaalde manier te doen dat we niet beseffen dat het misschien niet de beste manier is. Je moet al je processen dus kritisch onder de loep nemen. Dat gaat over het maken van offertes, voorraadbeheer, facturatie, planning, productie en communicatie, … alle schakels in je proces.”
“Goed is daarbij de vijand van uitstekend. Het moet een voortdurend proces worden waarbij je steeds weer gaat kijken wat misschien nog beter kan. Je mag niet blijven stilstaan. Vind je dat je al goed bezig bent, dan ga je niet meer verbeteren. Je wordt erin getraind om te leren zien dat zaken altijd nog beter kunnen.”
“Eens je zicht hebt op je verspillingen bestaan er verschillende tools om deze aan te pakken, zoals 5S, Standaard Werk, kanban, SMED of TPM. Het is vooral belangrijk om de basis van dergelijke tools te begrijpen zodat je ze naar je hand kunt zetten. Tijdens een traject gaan we er heel hands-on mee aan de slag op de werkvloer. En nog belangrijker: je moet ervoor zorgen dat de veranderingen die je hebt doorgevoerd, blijvend zijn. Dat is een uitdaging, want we grijpen snel terug naar hoe het vroeger was.”
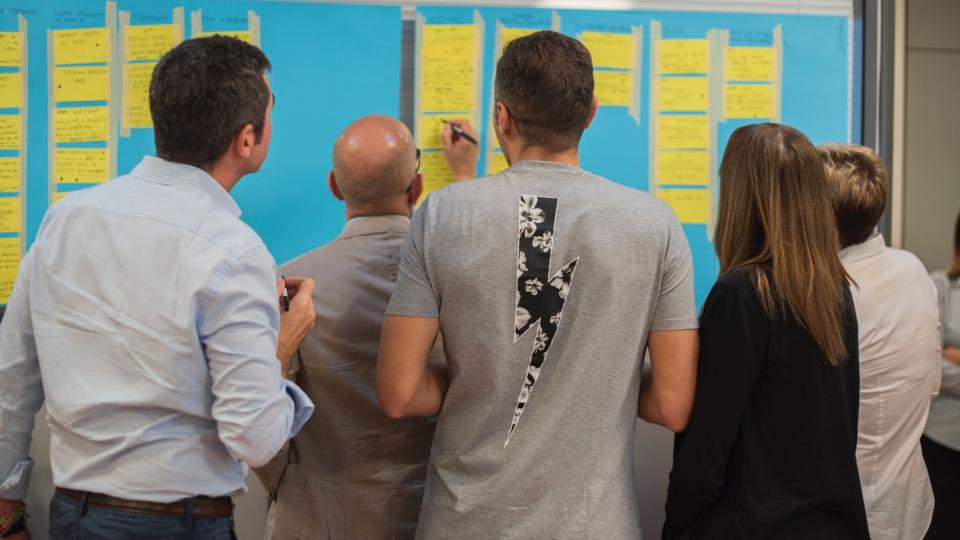
Je medewerkers betrekken is cruciaal
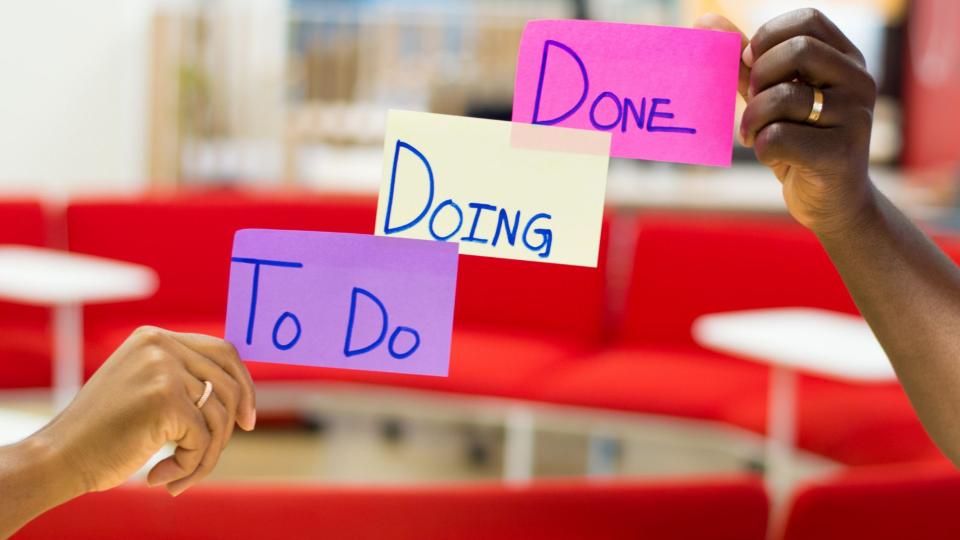
Breng flow in je processen
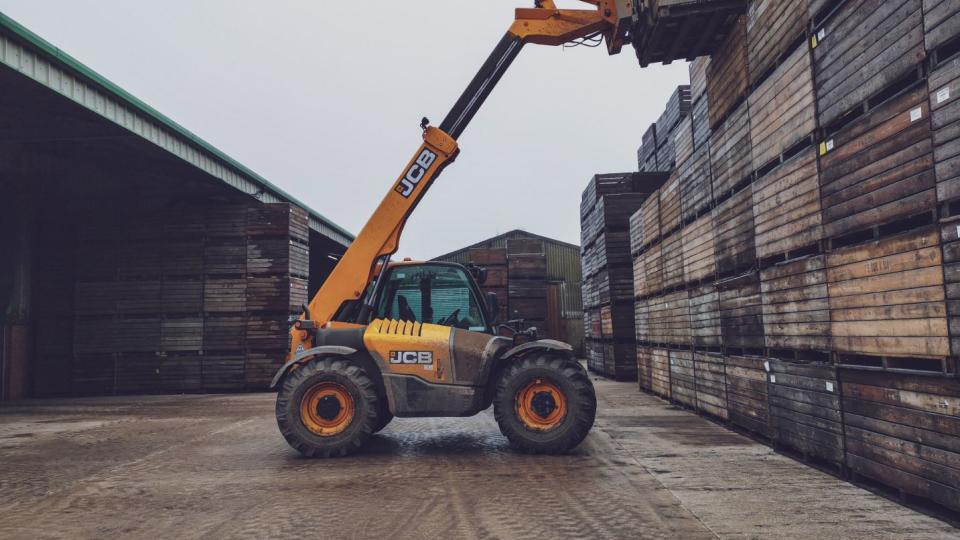
Zorg voor minder verspilling, verbeter de doorstroom van materialen
Hoe kan je er dan voor zorgen dat verbeteringen blijvend zijn?
“Pas als je erin slaagt om je medewerkers in de flow te brengen, zullen veranderingen blijvend zijn. Dat is waar de kennis zit hé, op de werkvloer.”
“Je doet dit door hen te betrekken bij elke stap in het proces. Je kunt je niet voorstellen wat je dan terugkrijgt. Je legt het probleem voor, geeft enkele principes mee en ze zijn vertrokken. De ene leidinggevende is er sneller mee weg dan de andere, en een coachende houding aannemen is hierbij heel belangrijk. Tijdens een traject organiseren we workshops waarbij we samen met de medewerkers een hele dag lang op de werkvloer dingen doen en uitproberen.”
Stel dat ik als vakman stappen wil zetten richting Industrie 4.0. Is er een ideaal moment in zo’n traject om je deze filosofie eigen te maken?
“Iedereen zal er op elk moment baat bij hebben, maar je doet het sowieso best voor je gaat investeren. Ik heb het wel vaker zien gebeuren dat bedrijven na een training tot heel andere investeringsplannen komen. Ze beseffen dan dat investeren in een bepaalde tool of machine niet alle problemen gaat oplossen, of ze zien dat er andere oplossingen zijn die misschien minder kosten.”
Christine is zeker voorstander van automatisering, maar weldoordacht. “Je moet een goede basis vinden, zelfs bedrijven als Toyota en Volvo hebben een stap terug gezet op vlak van robotisering omdat ze het menselijke brein misten als er problemen moesten worden opgelost. Dat kan een robot niet, maar hij kan het werk wel gemakkelijker maken.”
Al te vaak wordt er eerst geïnvesteerd in software die – toegegeven – heel veel kan, maar vooral veel zaken die je niet nodig hebt. Ze zeggen dan dat je jouw processen aan de software moet aanpassen, maar het is omgekeerd.
Dus eerst je proces vereenvoudigen en dan pas investeren in software en machines?
“Je moet eerst heel goed weten hoe je wilt werken. Pas nadat je je processen in kaart hebt gebracht én ze hebt geoptimaliseerd, ga je kijken hoe je deze kunt ondersteunen. Al te vaak wordt er eerst geïnvesteerd in software die – toegegeven – heel veel kan, maar vooral veel zaken die je niet nodig hebt. Ze zeggen dan dat je jouw processen aan de software moet aanpassen, maar in feite is het omgekeerd. Eerst moet je de basis in orde krijgen en dan pas ga je op zoek naar systemen en tools die daarbij passen.”
Wat zijn typische problemen waarbij het flow denken kan helpen?
“Het kan bijvoorbeeld helpen bij het verkorten van de doorlooptijd, zodat je een project daadwerkelijk kunt opleveren wanneer je het beloofd hebt. Je leert je voorraad optimaliseren, want je wilt niet te veel op voorraad hebben. Je gaat vergissingen minimaliseren, zoals een verkeerde maatvoering of een foutief onderdeel gebruiken, of bepaalde zaken vergeten bestellen of niet meenemen naar de werf. Soms zijn er te veel bewegingen op een werkvloer, en dat pakken we dan aan door de lay-out op de productievloer aan te passen.”
Is een zo laag mogelijke voorraad ook vandaag nog aangeraden, gezien de huidige situatie?
“Het is een menselijke reflex om nu een grotere voorraad te willen aanleggen, zeker als je buren het ook doen, maar daardoor ontstaat er een sneeuwbaleffect. Door meer in te slaan dan je nodig hebt, creëer je schaarste wat de prijzen op zijn beurt ook weer verder de hoogte in jaagt. Je wordt bijna verplicht vandaag, maar het kost je dubbel. Eén keer omdat je geld vast zit in je voorraad en een tweede keer omdat de prijzen verder zullen blijven stijgen.”
Is het flow denken al ingeburgerd in de schrijnwerksector?
“Het is nog relatief onbekend terwijl vooral KMO’s er zeer snel positieve resultaten mee kunnen boeken. Hoe groter een bedrijf, hoe minder efficiënt alles vaak verloopt en hoe talrijker de problemen zijn. De communicatie verloopt moeizaam en de reactiesnelheden zijn te traag. Je hebt typisch een afdeling HR, finance, engineering, productie, kwaliteit… met dikke muren tussen die verschillende afdelingen. Nog voor je de nodige goedkeuringen bij elkaar hebt om je probleem aan te pakken, is het kalf vaak al verdronken. Dat speelt niet alleen bij bedrijven, maar ook bij scholen en zelfs gemeenten. Een klein bedrijf is wendbaarder.”

Optimaliseer de bewegingen op de vloer
De kunst bestaat erin om toch in zekere mate afstand te nemen om zo een helikopter view te krijgen en tijd vrij te maken voor strategisch denken. Hoe gaan we bepaalde zaken verbeteren en welke richting gaan we uit?
Moeten we dat zien als een pleidooi tegen groei?
Groeien mag uiteraard, maar je moet het op de juiste manier doen. Dan kom je bij het QRM-principe, of het Quick Response Manufacturing. Je vormt dan kleinere teams binnen je organisatie die autonoom werken en zelf beslissingen kunnen nemen. Op die manier blijf je wendbaar.”
Schrijnwerkers werken hard en zijn meestal heel erg betrokken bij het productieproces. Is dat een valkuil?
“Het is voor hen vaak een ongelooflijke uitdaging om tijd vrij te maken voor zo’n training. Ik heb mensen gezien die zo overwerkt waren, die dag en nacht werkten en nog niet alles gedaan kregen. De kunst bestaat erin om toch in zekere mate afstand te nemen om zo een helikopter view te krijgen en tijd vrij te maken voor strategisch denken. Hoe gaan we bepaalde zaken verbeteren en welke richting gaan we uit? Van de andere kant is het zeker niet verkeerd om er helemaal in te staan. Dan begrijp je heel goed wat de reële situatie is.”
Dan moet je eerst wel mensen vinden aan wie je werk kunt doorspelen. Het personeelstekort is groot?
“Dat is inderdaad een enorme uitdaging. De Lean filosofie zal er wel voor zorgen dat je minder arbeidsuren nodig hebt om het werk uit te voeren. Je zult je mensen geen taken meer laten uitvoeren die geen waarde toevoegen en zo efficiënt mogelijk werken. Je zult dus minder snel extra mensen nodig hebben, maar als je ze dan nodig hebt, zijn ze vandaag moeilijk te vinden. Dat is helaas zo.”
Snel dit artikel gratis lezen?
Maak eenvoudig en gratis een account aan.
-
Lees elke maand een aantal plus-artikels gratis
-
Kies zelf welke artikels je wil lezen
-
Blijf op de hoogte via onze nieuwsbrief
- Na het enorme succes van de Master Oak-collectie, voegt Unilin Panels nu 12 nieuwe, indrukwekkende decors toe aan het bestaande gamma…
Hoogwaardige houtverbindingen voor elk bouwproject
Bent u op zoek naar de meest betrouwbare en efficiënte oplossingen voor uw houtbouwprojecten? Zoek niet verder! Ontdek de betrouwbare…Woema: “BIM is essentieel voor het succes van prefab-projecten”
Woema verliet het Gala van de Gouden Baksteen met de award voor digitale onderneming van het jaar onder de arm. Het bedrijf zegt aan …Voor- en nadelen van kwartscomposiet werkbladen
Kwartscomposiet werkbladen, ook bekend als kwarts keukenbladen of composiet werkbladen, zijn gemaakt van een van de hardste mineralen ter…

Lees de laatste editie nu gratis online
Kantoor Showroom LamettHoreca Beursstand Keukens De AbdijOnderwijs Optopping atheneum MariakerkeKantoor Apotheek in CLTKantoor Totaalinrichting optiekzaakResidentieel Renovatie herenhuisResidentieel Totaalinrichting particuliere woningKantoor Totaalinrichting kantoor EuropabankResidentieel Thuiswerkplek 2.0Residentieel Keuken in sixties-sfeer