La machine de nesting: le meilleur choix ou pas? Et pour qui?
"Cela fait deux ans que nous utilisons une machine de nesting, à savoir une SCM X 200 à trois axes", explique Frans Maenhout, directeur de l'entreprise éponyme. "Nous pouvons également encore recourir à une scie à panneaux ainsi qu’à une machine CNC, mais nous ne le faisons pratiquement plus."
Collègue-concurrent et fournisseur de la Cour, Van Overstraeten possède quant à lui déjà 10 ans d'expérience dans le nesting. "Depuis le début, nous travaillons avec une machine de nesting équipée d’un plateau de déchargement. Depuis deux ans, il s’agit d’une nouvelle machine à cinq axes avec plateau de déchargement Holz-Her", explique Joachim Van Overstraeten, qui représente la cinquième génération de cette entreprise familiale. Van Overstraeten et Maenhout disposent aussi tous deux d’un magasin automatique avec empileur.
L’entreprise Integral, par contre, a délibérément opté pour une scie à panneaux et une machine CNC. Pourquoi? C’est la question que nous poserons à Pablo Verschaere d'Integral. Nous avons d’abord déambulé dans les ateliers de Maenhout et Van Overstraeten. Comment utilisent-ils le nesting, et qu'est-ce que cela leur rapporte?
Qui est qui?
- Maenhout Wooninrichting produit principalement des intérieurs: cuisines, placards d’intérieur, dressings, meubles de salles de bains, etc. A côté de cela, l'entreprise réalise également des travaux de menuiserie tels que châssis, escaliers standard, portes (intérieures) et annexes en chêne.
- Van Overstraeten se charge de tout l’aménagement intérieur possible: également du mobilier pour cuisines, salles de bains, livings... Mais aussi, par exemple, des portes intérieures, des escaliers, des lambris.
- Integral conçoit, produit et installe des aménagements de magasin complets pour les boulangeries, chocolatiers, boucheries, traiteurs et poissonniers. De A à Z. De la conception à la livraison.
A l’ouvrage avec une machine de nesting
Tout commence par une discussion avec le client, pour connaître le mobilier et l'aménagement souhaités. Une fois le premier concept approuvé, dans le cas d’un placard par exemple, Maenhout et Van Overstraeten réalisent un dessin technique dans leur logiciel de CAO/FAO. Une fois que le client a également approuvé ce dessin, le programme génère les listes de pièces et élabore les plans de production. Par panneau, le logiciel calcule comment la machine de nesting pourra débiter toutes les pièces par fraisage, suivant une composition optimale avec le moins de pertes possible.
"Chez nous, le logiciel prélève ensuite les panneaux un par un dans le magasin automatique", poursuit Frans Maenhout. "De là, le matériau roule sur la bande transporteuse jusqu'à la station d'étiquetage, afin d’y coller des étiquettes avec des informations concernant le chant nécessaire, la dénomination de la pièce, les dimensions, les remarques du dessinateur, etc."
"Dans notre cas, c’est la machine de nesting qui procède elle-même à l’étiquetage", poursuit Joachim Van Overstraeten. "Pour chaque commande, l'opérateur reçoit un dossier contenant, entre autres, les numéros d’emplacement et de position des panneaux à travailler. Il les sélectionne ensuite, après quoi notre magasin automatique empile assez rapidement les panneaux. Puis, l'opérateur introduit les panneaux un par un dans la machine de nesting."
Lisez aussi
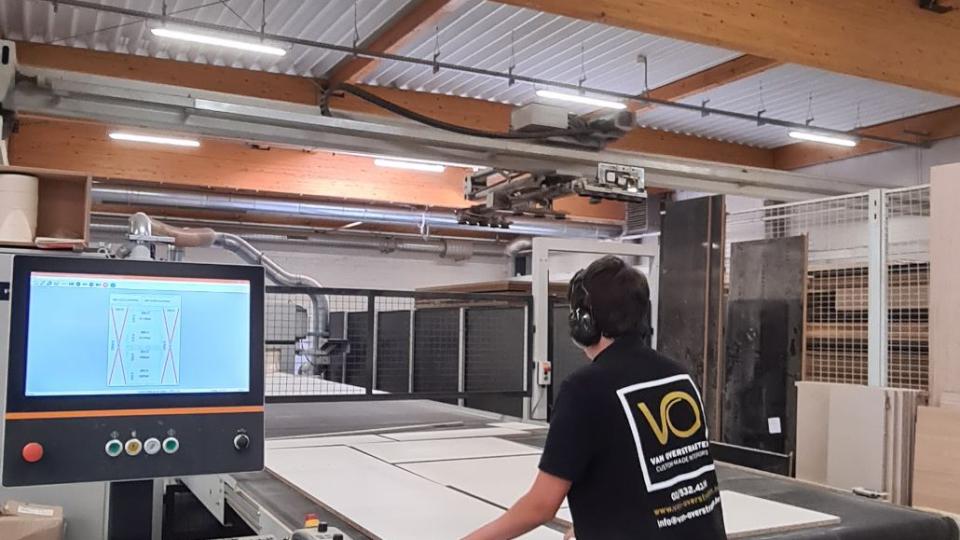
La machine de nesting de Van Overstraeten
Compositions de fraisage optimales
"La machine de nesting commence par percer tous les trous verticaux. Elle débite ensuite les pièces nécessaires dans le panneau par fraisage, puis elle pousse le panneau vers le plateau de déchargement, où nous empilons les pièces fraisées", explique Joachim. "Chez nous, une fois le panneau fraisé et percé, il se retrouve à nouveau sur une bande transporteuse", ajoute Frans Maenhout, "après quoi nous le déchargeons." Les pièces fraisées sont alors prêtes à passer à la plaqueuse de chants pour la finition des bords.
Une production triplée
Maenhout usine à la machine de nesting pas moins de 80% de ses panneaux mélaminés (d'une épaisseur de 10, 18 et 25 mm). "Quand tout va bien, nous pouvons fraiser 40 à 50 panneaux mélaminés par jour pour débiter les pièces nécessaires", résume Frans. "Nous transformons environ 30 panneaux par jour", réagit Joachim Van Overstraeten. Dans les deux cas, il s’agit d’une grande différence par rapport à avant. "Nous avons triplé notre production", déclare Frans.
"Auparavant, nous devions d'abord aller chercher les panneaux dans l’entrepôt avec un chariot élévateur. Ensuite, nous les placions un par un sur la scie à panneaux pour les débiter section par section", poursuit Frans. "Une opération qui exigeait de placer le panneau dans le bon sens à plusieurs reprises", ajoute Joachim. "Maintenant, c’est la fraise qui se déplace tandis que le panneau reste en place, et vous obtenez directement toutes les pièces, en plus munies de tous les perçages. C’est non seulement beaucoup plus rapide, mais cela réduit aussi les risques de rayures car vous ne devez plus retourner les panneaux."
Également moins de déchets
Le nesting produit aussi moins de déchets. "Toutes les pièces de moins de 2 x 1 m retournent à l'entrepôt. Lors d’un projet ultérieur, notre logiciel de CAO/FAO utilisera ces pièces en premier lieu, si possible. Toutes les pièces de moins de 1,5 m x 70 cm atterrissent dans un rayonnage, et serviront par exemple pour des petites réparations", explique Frans Maenhout.
De plus, le logiciel calcule toujours la découpe optimale, avec le moins de déchets possible. "La scie à panneaux entraîne des pertes plus importantes", affirme Joachim Van Overstraeten, "parce qu’il faut toujours travailler avec des coupes longues, même lorsque vous avez besoin d’une pièce plus courte." À moins que vous n'optimisiez davantage la composition, mais il vous faudra alors retourner davantage le panneau, ce qui augmentera le nombre d'heures de travail.
Encore parfois la scie à panneaux et la machine CNC
Parfois, Maenhout et Van Overstraeten utilisent encore la scie à panneaux et la machine CNC. "Surtout pour les pièces plus petites et plus étroites, comme les plinthes de 10 cm de largeur", explique Joachim Van Overstraeten.
"En effet, celles-ci se détachent plus facilement sur la machine de nesting. Dans le même temps, nous débitons sur la scie à panneaux des pièces plus épaisses, de 38 ou 50 mm. Cela pourrait aussi se faire sur la machine de nesting, mais il nous faudrait pour cela acheter une fraise spécifique."
"Nous utilisons également la scie à panneaux et la machine CNC pour les couches de placage spéciales, lorsque le motif doit se prolonger. Lorsque vous les fraisez sur une machine de nesting, cela enlève trop de bois."
Pour d'autres applications également, la fraise fait perdre trop de surface. "Il est en soi parfaitement possible, par exemple, de produire des encadrements de porte avec la machine de nesting", précise Frans Maenhout. "Mais lorsque vous fraisez des encadrements de 16 cm de large par exemple, vous perdez dix fois la largeur de la fraise, soit dans notre cas 12 cm en tout."
Nous avons vite compris que nous allions amortir cet investissement. Quand tout va bien, nous pouvons fraiser 40 à 50 panneaux mélaminés par jour pour débiter les pièces nécessaires.
A prendre en compte: le nesting requiert beaucoup d'énergie (et de l'argent)
Autre aspect non-négligeable: le nesting requiert beaucoup d'énergie. "A l’instar d’une machine CNC, une machine de nesting fixe le panneau par serrage à vide", explique Frans. "Pour ce faire, notre installation a besoin de 1.000 m³ de vide. En compagnie du vide pour la machine CNC, cela représente une facture d’énergie mensuelle de 9.000 euros."
"A côté de cela, la fraise de la machine de nesting doit être remplacée plus rapidement que la lame d'une scie à panneaux. Avec notre rythme de travail, les fraises durent deux à trois semaines, contre deux à trois mois pour les lames de scie." Même son de cloche chez Van Overstraeten.
La machine de nesting a coûté environ 145.000 euros à Maenhout. À côté de cela, l'entreprise a également acheté un magasin automatique, de même qu'une nouvelle table de montage et une station d'étiquetage, une pompe à vide supplémentaire de 500 m³, le logiciel de CAO/FAO qui pilote le tout... "Soit un investissement de 500.000 euros en tout", se souvient Frans. "Notre machine de nesting nous a coûté 180.000 euros", indique Joachim Van Overstraeten. "Nous avions déjà notre magasin automatique."
"Nous avons vite compris que nous allions amortir cet investissement", souligne Frans Maenhout. "En cinq ans normalement, alors que la machine fonctionne moins de huit heures." Chez Van Overstraeten, on estime que le délai d’amortissement sera un peu plus long: un peu moins de sept ans.
Pas de nesting, un choix délibéré
Contrairement à Maenhout et Van Overstraeten, Integral a délibérément choisi de ne pas recourir au nesting. Pourquoi?
"Nous disposions d’une machine CNC à quatre axes et d’une scie à panneaux", explique Pablo Verschaere d'Integral.
"Toutes deux avaient cependant besoin d'être renouvelées. Le nesting nous semblait une option intéressante, surtout en termes de rendement, mais il ne correspondait pas vraiment à notre travail. D'une part parce que les machines de nesting offrent une capacité trop importante pour nos besoins, et d'autre part parce que nous n’assemblons pas que des placards, mais devons aussi fraiser régulièrement de très grandes pièces, pour lesquelles nous aurions dû modifier les réglages de la machine chaque semaine. Ou bien des pièces très complexes, avec des onglets arrondis, des limons courbes, de nombreux usinages d’about... Une machine CNC à cinq axes avec ventouses et barres restait indispensable, car elle permet aussi de fraiser parfaitement des arrondis."
Pour nos activités, une machine CNC à cinq axes avec ventouses et barres restait indispensable.
Nouvelle machine CNC, scie à panneaux et plaqueuse de chants
Integral a donc décidé d'investir dans une nouvelle machine CNC. "Notre Format-4 H500 S-Motion offre cependant un champ d’applications plus important. De plus, les ventouses et barres se positionnent automatiquement aux bons endroits. Ce qui nous a permis de réduire nos temps de réglage de plus de la moitié."
D'autre part, Integral a acheté une nouvelle scie à panneaux, une Mayer PS 80 Premium, ainsi qu'une nouvelle plaqueuse de chants. Integral dessine également tout dans un logiciel de CAO/FAO, qui pilote entièrement les machines, suivant une préparation minutieuse de la production.
Integral a également envisagé d'installer un magasin automatique. "Mais nous réalisons un aménagement de magasin par semaine, de telle sorte que nous utilisons des panneaux différents semaines après semaines. Nous utilisons bel et bien deux matériaux standard pour les corps de meuble, mais grâce à un nouvel élévateur, ces deux matériaux sont toujours disponibles de stock sur nos machines."
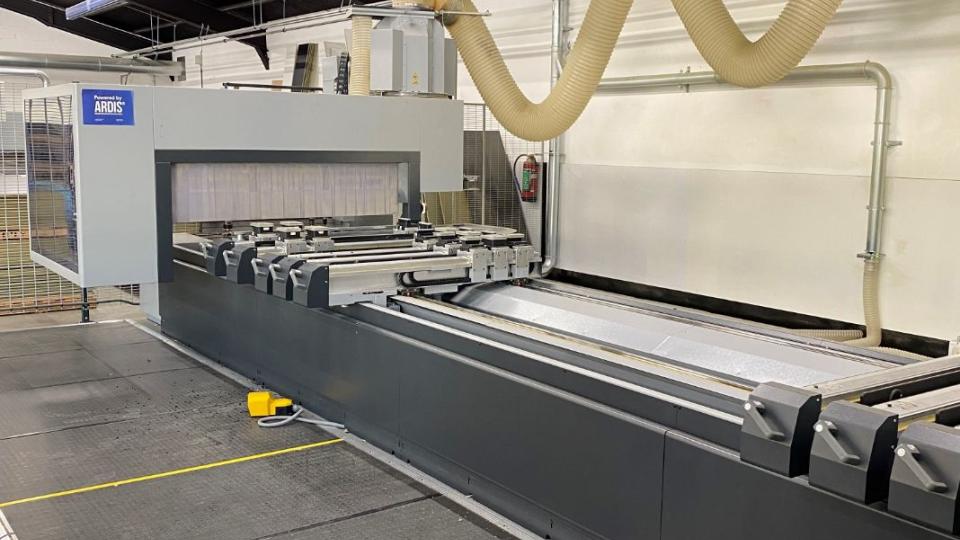
La machine CNC d’Integral: un choix délibéré
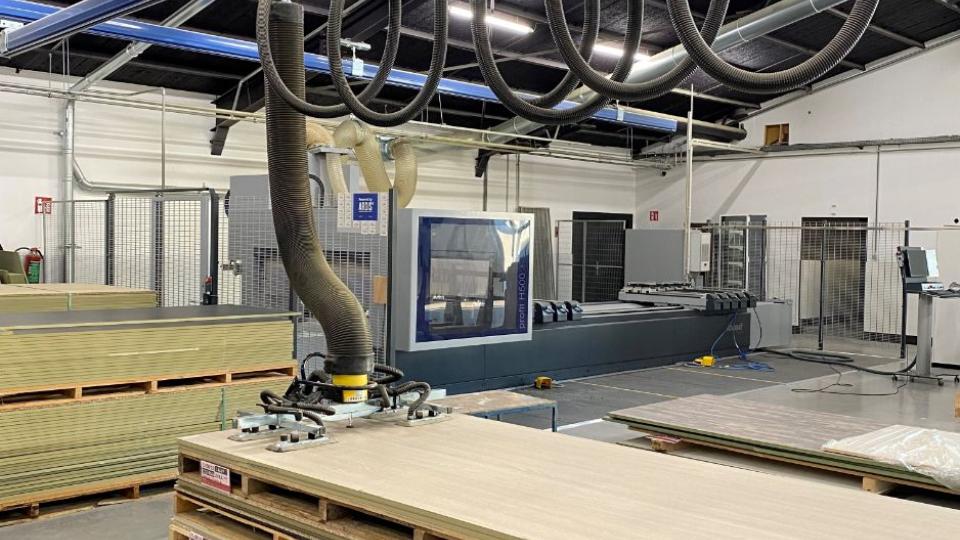
Système d’élévateur chez Integral, grâce auquel les matériaux standard sont toujours disponibles de stock pour chaque machine.
Des temps au défilé tout de même plus courts
Grâce aux nouvelles machines, Integral a tout de même réussi à réduire ses temps au défilé, parfois même jusqu'à 70%, indique Pablo.
"Cela s’explique surtout par le rendement supérieur des nouvelles installations. Notre scie à panneaux débite beaucoup plus rapidement les panneaux sans perte de qualité, et ce avec des lots beaucoup plus importants. Notre machine CNC est quant à elle plus longue, ce qui nous permet d’usiner simultanément des panneaux entiers à gauche et à droite. Et notre plaqueuse de chants est équipée d’un système de retour de pièce automatique, et ne nécessite plus la moindre opération de nettoyage. Les trois machines peuvent être pilotées par un seul et même opérateur."
En même temps, Integral a également réussi à élever le rendement de ses panneaux de 8%, grâce à un meilleur contrôle du stock et des déchets résiduels. "Les éléments restants sont étiquetés et placés dans des rayonnages près de nos machines. Lorsqu’une chute peut être utilisée, le logiciel l'indique."
La conclusion?
Le meilleur choix variera en fonction de l’entreprise et son activité. Quelle est votre activité principale? Aurez-vous suffisamment besoin de la capacité et des possibilités qu’offre le nesting? Et en combien de temps la machine de nesting s’amortira-t-elle? Tout tournera autour de cela.