Hoe geconnecteerd en transparant zijn jouw machines?
Het project kwam er omdat ze merkten dat heel wat bedrijven met vragen zitten. Het lijkt voor velen nog een ver-van-mijn-bedshow, maar net daar wil Sirris verandering in brengen. “We willen de drempel voor bedrijven verlagen,” vertelt Jakob, “door duidelijk te maken wat connected manufacturing concreet inhoudt, wat de voordelen zijn en hoe je ermee aan de slag gaat. We willen bedrijven inspireren zodat ze merken dat ieder bedrijf er zijn voordeel uit kan halen, ook kleinere KMO’s.”
Hij omschrijft dit mooi als de democratisering van de technologie. Het project wordt gesteund door VLAIO en naast Sirris werkt ook Flanders Make er aan mee.
Connected manufacturing voor beginners
Wat moeten we ons nu precies voorstellen bij zo’n geconnecteerde productieomgeving? Alles draait om het verbinden van machines en bedrijfsapplicaties om zo de productiviteit en de transparantie te verhogen.
“Als je productie transparant is, weet je in real time wat er gebeurt en waarom”, vertelt Jakob. “Je kunt ingrijpen en gerichte verbeteracties ondernemen. Je productie wordt veel responsiever.”
Elke situatie is uniek, maar toch zijn er vier scenario’s die regelmatig voorkomen en die Sirris wil uitdiepen.
In de eerste plaats kan het gaan om het genereren van verschillende dashboards voor diverse toepassingen, die in (near) real-time een inzicht verschaffen in wat er gebeurt in de productie. “Zo’n dashboard kan ten dienste staan van het productiemanagement zodat ze kunnen inschatten hoe efficiënt alles verloopt, ten dienste van de operatoren om hen inzicht te bieden in de status van de productie, of beiden. Je kunt het ook gebruiken om bottlenecks te identificeren en aan te pakken.”
Als je productie transparant is, weet je in real time wat er gebeurt en waarom. Je kunt ingrijpen en gerichte verbeteracties ondernemen
Transparante productie
Een tweede mogelijkheid is de terugkoppeling van gegevens van de productievloer naar het bestaande ERP-systeem zodat men de planning kan afstemmen op de actuele toestand van de productie.
“In heel wat bedrijven wordt er al een order gecreëerd in een ERP-systeem, maar eens het in productie gaat, heb je er geen zicht meer op tot het order gefinaliseerd is. Dit levert heel wat problemen en discussies op wanneer je de status van een bepaald order wil gaan checken op de vloer. Dit transparant maken zorgt er ook voor dat je de capaciteit veel beter zult kunnen inschatten. Je kunt meteen zien waar je nog marge hebt voor eventuele extra orders en waar capaciteitsproblemen zitten. Je moet niet meer raden naar de bezettingsgraad en wat je kunt doen om je efficiëntie te verhogen.”
Een voorbeeld maakt het nog duidelijker. Zo was Jakob betrokken bij een project voor Renier Natuursteen: “Hun productie verliep al vrij sterk geautomatiseerd. Er waren twee robotopstellingen waarbij de ene robot zorgde voor de belading van een machine, de andere voor de verdere afwerking van de stenen. Alles tussen die twee stappen was voor het bedrijf echter nog een ‘black box’. Zonder in te gaan op de technische details heeft hun traject ervoor gezorgd dat men nu van elk pallet weet welke stukken erop staan, waar deze zijn geweest en ook waar ze naartoe moeten. Uit de data kunnen ze nu ook opmaken hoe efficiënt de productie is en wanneer er een onderdeel is dat een storing vertoont. Doordat de status van de productie op ieder moment bekend is, kan corrigerend worden ingegrepen, met als resultaat een verbeterde productiviteit en efficiëntie.”
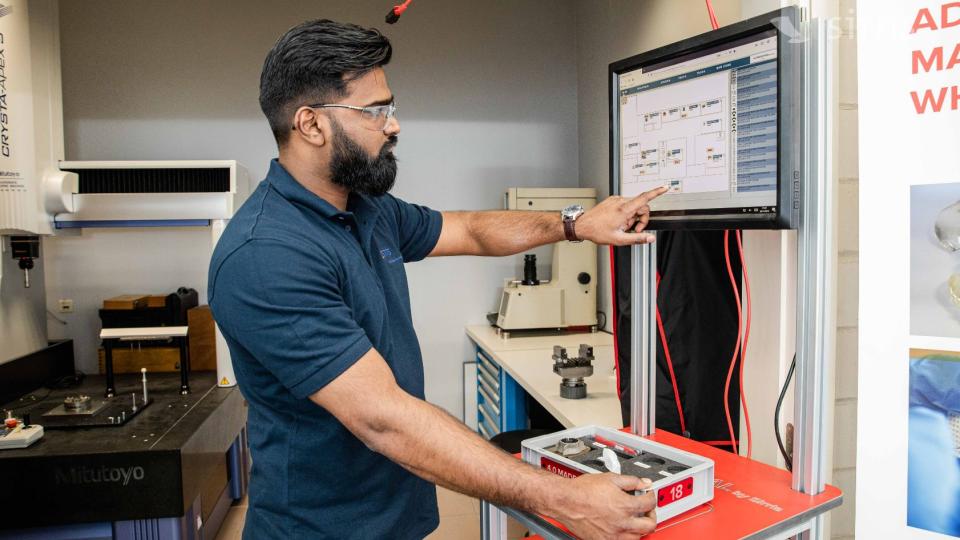
Maak je productie transparant met connected manufacturing
Efficiëntere machines en operatoren
Een derde mogelijkheid is de uitwisseling van data tussen maakbedrijf en machinebouwer/integrator voor het opstarten van digitale diensten door machinebouwers of integratoren voor klanten. “Iets waar bedrijven niet altijd voor staan te springen, tot ze voelen dat hun machines efficiënter worden door het te doen.”
En tot slot het optimaal inzetten van productiegegevens voor een meer gerichte aansturing van operatoren. Dit was bijvoorbeeld het geval bij Aluro CNC. “De operatoren werden er voortdurend getriggerd”, licht Jakob toe. “Ze moesten continu rondkijken of batches op hun machines aflopen, of uitkijken voor productiestilstand. Dat was voor hen behoorlijk stresserend. Door data van de verschillende machines en robots te capteren en weer te geven op een dashboard werd de productie een stuk transparanter zodat operatoren een beter zicht hebben op wat er wanneer gaat gebeuren.”
“Elke operator kreeg een tablet waarop hij de productiestatus kan zien van de machines waarvoor hij verantwoordelijk is. Hij kan nu bijvoorbeeld zien dat een bepaalde machine binnen vijf minuten klaar is en dat hij dus nog even iets anders afronden voor hij ermee aan de slag moet. De impact van de geconnecteerde productievloer is hier vooral gevoelsmatig: het werk op zich verandert niet, maar de operatoren hebben nu vat op het proces. Daarnaast kan het bedrijf nu ook sneller inspelen op problemen of stilstand.”
Een systeem moet zowel voor het management als voor de operatoren voordelen opleveren. De beste resultaten bereik je door alle stakeholders bij het proces te betrekken, ook de mensen op de productievloer
Werknemers betrekken: een vereiste
Bij Aluro CNC stond het welzijn van de operator centraal, maar dat is niet altijd het geval. Meer nog, in sommige gevallen ervaren de werknemers de veranderingen als een extra belasting en niet als een stap vooruit.
“Dan zijn wij soms de kritische stem in het traject, die het management ook doet stilstaan bij de impact op de mensen op de werkvloer. Een systeem moet zowel voor het management als voor de operatoren voordelen opleveren. De beste resultaten bereik je door alle stakeholders bij het proces te betrekken, ook de mensen op de productievloer. Ze weten wat er speelt en hebben meestal goede ideeën. Door hen erbij te betrekken, raken ze ook meteen gemotiveerd.”
Niet connecteren om te connecteren
Daarnaast moet je ook heel helder hebben waarom je de productievloer wil gaan connecteren.
“Een geconnecteerde productievloer mag geen doel op zich zijn”, vertelt Jakob. “Je moet er niet mee starten omdat je het steeds meer bedrijven ziet doen, maar omdat het je helpt om bepaalde uitdagingen aan te pakken. Er zijn effectief bedrijven die hier de bal hebben misgeslagen en die nu heel veel data uit hun productie halen waar ze vervolgens niets mee doen.”
Gebruik wat je bij andere bedrijven ziet met andere woorden als bron van inspiratie, maar vermijd klakkeloos kopiëren.
“Onze eerste stap is altijd nagaan of het connecteren van de productie voor een bedrijf voldoende meerwaarde heeft. Soms kunnen ze eerst beter andere stappen zetten, maar ik denk wel dat iedereen – gaande van schrijnwerkers die nog manueel werken tot bedrijven die al investeerden in computergestuurde machines – op zijn maat stappen kan zetten richting digitalisatie. Je moet jezelf een digitale mindset aanmeten en dat is niet evident. Een bedrijfscultuur verander je niet van vandaag op morgen. Ik moet denken aan een bedrijf dat een fantastisch digitaal planningssysteem op poten had gezet, maar het toch moest terugdraaien omdat de operatoren het niet gebruikten. Soms werken kaartjes, die visueel op prioriteit worden gerangschikt, beter.”
Vergewis je er dus van dat je bedrijf klaar is voor de nieuwe technologie die je wil introduceren, geeft Jakob aan. Investeer niet alleen in systemen, maar indien nodig ook in opleiding en coaching. Daar komt ook bij dat je als bedrijf wat ruimte moet hebben om de opgedane kennis ook te absorberen. “Zeker na covid zijn er heel wat bedrijven die nu al hun resources nodig hebben voor het operationele. Wil je dat de veranderingen echt blijvend zijn, dan moet je er wel wat tijd in kunnen investeren.”
Ook bij oudere machines kan je via de aanwezige interfaces vaak de gewenste data gaan capteren. Je kunt perfect één machine connecteren en daar al voordeel uithalen.
Voor elk machinepark?
Of en in welke mate een machinepark geconnecteerd kan worden, is een erg uniek gegeven.
“Het is steeds opnieuw bekijken wat de opties zijn”, vertelt Jakob. “Soms is het een combinatie van ‘legacy’ en nieuwe machines en moet je gaan bekijken welke protocollen je kunt gebruiken en hoe je de data kunt gaan capteren. Wij ijveren daarbij voor open standaarden zodat je machinepark flexibel, modulair en uitbreidbaar blijft, en je niet afhankelijk bent van een bepaalde machinefabrikant.”
Anders dan je misschien zou verwachten hoef je absoluut niet de meest hoogtechnologische machines in huis te hebben om hiermee aan de slag te gaan.
“Ook bij oudere machines kan je via de aanwezige interfaces vaak de gewenste data gaan capteren. Je kunt ook perfect één machine connecteren en daar al voordeel uithalen.”
Connected manufacturing en andere technologische innovaties zijn dus zeker niet alleen voor de grotere bedrijven weggelegd. “Eén van onze klanten omschreef het zo: ‘hoe kleiner je bedrijf, hoe gemakkelijker je kunt omschakelen’. Dat klopt helemaal. In een groter bedrijf moet je veel meer kritische massa verplaatsen, terwijl je als kleiner bedrijf op korte termijn kunt schakelen.”
Wat levert het op?
Een vraag die op ieders lippen brandt, vertelt Jakob. Bedrijven willen heel graag vooraf weten wat de investering hen zal opleveren.
“We zijn dan ook een methodiek aan het uitwerken om ROI-berekeningen te ondersteunen. Een exact cijfer zal en kan daar nooit uitkomen, want er zijn altijd factoren die je niet kunt voorzien. Vaak merk je ook pas later dat er nog bepaalde voordelen zijn die je nooit had kunnen anticiperen. Heel lang blijven stilstaan bij dergelijke cijfers, levert niet altijd veel op. Ik ben nogal voor de pragmatische aanpak: welke voordelen levert het op en wat staat je te wachten als je het niet doet?”
Boeiende vragen waar je alvast even bij kunt stilstaan.
Snel dit artikel gratis lezen?
Maak eenvoudig en gratis een account aan.
-
Lees elke maand een aantal plus-artikels gratis
-
Kies zelf welke artikels je wil lezen
-
Blijf op de hoogte via onze nieuwsbrief